El sistema doeet® ha sigo elegida junto con Grupo IPYC por la Universidad de Milán para desarrollar el proyecto europeo Cyber Physical Production System for Zero Defect Manufacturing (CPPS4ZDM) junto a centic (Centro Tecnológico de las Tecnologías de la Información y las Comunicaciones de Murcia) para la empresa Jalsosa (Granada, España).
Por este motivo David Fuster, CTO de doeet® realizó una ponencia en el transcurso del Fiware Tech Summit celebrado en Málaga el pasado 28 y 29 de noviembre de 2017.
La iniciativa Cyber Physical Production System for Zero Defect Manufacturing intenta relacionar la calidad del producto final con otras variables de la producción.
Para ello adoptaremos tecnologías Big Data, inteligencia Artificial e IOT (Internet de las cosas) para el análisis masivo de datos utilizando las tecnologías de la plataforma Fiware. La fundación Fiware provee una serie de tecnologías, infraestructuras y redes de servidores cloud con una alta capacidad de computación.
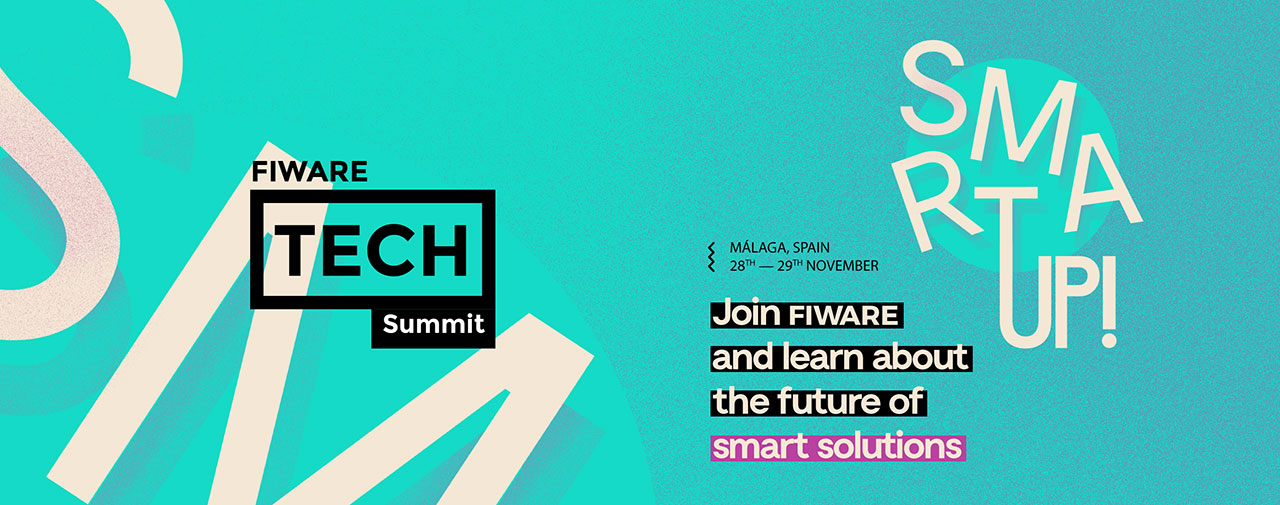
Objetivos del proyecto
El objetivo del proyecto CPPS4ZDM es introducir CPS en el mundo del taller de mecanizado tradicional para resolver un requisito de gestión de cero defectos. El proyecto demostrará que es posible administrar los datos de los operadores obtenidos de máquinas y plantas con una combinación inteligente de sensores y datos de producción para resolver estos problemas.
La medición de parámetros y características críticas por CPPS (Cyber Physical Production Systems) permite medir características específicas (variables de productos o procesos) de manera apropiada y en tiempo real, incluidos los operadores y las máquinas.
El desafío Zero Defect Manufacturing requiere una combinación de técnicas estadísticas, de ingeniería y aspectos organizativos donde las herramientas TIC desempeñan un papel importante de cohesión en el equipo de la fábrica. De hecho, los operadores miden las características importantes de los materiales o el proceso de producción para determinar si el proceso todavía está «bajo control», lo que significa que la variación no es más de lo esperado y permitido.
El caso de uso involucra el proceso de fabricación de esponjas jabonosas con gel hipoalergénico y dermatológico para fines médicos y estándares de alta calidad en el sector de la Salud. Las esponjas, uno de los productos fabricados por JALSOSA, están impregnadas de una fórmula química que protege las pieles del paciente con una solución. Los principales clientes son los hospitales del sector de la salud y exigen una producción sin defectos.
Alcance del proyecto
Los principales resultados y alcance del trabajo son los módulos de software cubiertos por las aplicaciones CPPS4ZDM y doeet® que se utilizarán durante el experimento en las instalaciones de Jalsosa:
- Control de calidad de producción. Analizará la producción histórica (datos de calidad, datos del proceso, datos de la máquina, lagunas y alerta sobre condiciones de especificación probablemente fuera de servicio o bajo rendimiento en los niveles de la máquina).
- Optimizador de órdenes de producción para reducción de cero defectos. Analizará los tiempos programados de producción programados y alertará sobre condiciones de ruptura o bajo rendimiento en los parámetros de fuente de calidad, para obtener un sistema ZDM fácilmente manejado.
Los módulos de software se implementarán en una instancia de FIWARE en la nube, donde se instalará el tablero de instrumentos doeet®. Todos los CPPS relacionados, los sensores y sus conexiones se instalarán y desplegarán en las instalaciones del proyecto durante su ejecución para el objetivo de Zero Defect Manufacturing.
Zero Defect Manufacturing
El concepto de Zero Defect Manufacturing. se introdujo a principios de la década de 1960 y ahora es una práctica de fabricación común para reducir y minimizar el número de defectos y errores en un proceso y para hacer las cosas bien desde el principio. El objetivo final es reducir a cero el número de productos defectuosos. Sin embargo, el cero defectos significa cero fallos durante la operación, pero no necesariamente cero imperfecciones, imperfecciones o no conformidades.
Durante la década de 1990, las grandes empresas automotrices intentaron reducir los costos al reducir sus procesos de inspección de calidad y exigir a sus proveedores que mejoraran drásticamente la calidad de sus suministros. Esto eventualmente resulta en demandas para el estándar de cero defectos y este requerimiento se generalizó en todo el mundo.
Ahora el mercado obliga a las empresas a ajustar sus costes de producción y moverse a Just In Time (JIT) tanto como sea posible.
En este escenario, CPPS4ZDM es el experimento ideal basado en CPPS para gestionar la producción y permitir a las empresas mejorar la producción, la programación, la calidad, el mantenimiento y la documentación en un enfoque de fabricación con cero defectos.
Con la captura automática de sensores M.E.S., los datos CPPS4ZDM analizarán la información de los procesos, las máquinas, los horarios de los trabajadores, … utilizando indicadores internacionales como OEE (Eficiencia general del equipo) y todo en tiempo real reduciendo y mitigando los errores humanos.
Hoy día muchas PYMES todavía usan papel y bolígrafo para medir el proceso, y esta ineficiencia es aún mayor cuando los datos no son fáciles de analizar, o son muy subjetivos por parte de los trabajadores que agregan errores y defectos a la fabricación.
CPPS4ZDM será la herramienta para introducir la industria 4.0 a las PYMES y aprovechar las ventajas de la economía de escala de la nube. Teniendo en cuenta que ZDM (Zero Defect Manufacturing) es un requisito obligatorio del mercado para muchas de las PYMES, CPPS4ZDM demostrará que es posible cumplir con un costo reducido de implementación, con la ayuda de soluciones en la nube como FIWARE y BeinCPPS.
El caso Jalsosa
El caso de uso de Jalsosa involucra el proceso de fabricación de esponjas jabonosas con gel hipoalergénico y dermatológico para fines médicos y estándares de alta calidad en el sector de la Salud. Las esponjas producidas por Jalsosa, están impregnadas de una fórmula química que protege las pieles del paciente en una solución que ahorra costos. Los principales clientes son los hospitales del sector de la salud y exigen una producción sin defectos. La producción de esponja es fabricada por 3 procesos: fabricación de telas de fibra, impregnación y secado, corte y envasado.
Cada línea se monitorea y tiene varios controles de calidad (peso, densidad, temperatura, viscosidad, pH, dimensiones de longitud, …). Los operadores se encargan de las mediciones de parámetros de calidad tales como densidad, tamaño, peso, etc. Este proceso requiere mucho conocimiento, excelencia, coordinación y precisión en todos los aspectos del ciclo de vida del producto, desde la etapa inicial de recopilación de los requisitos del cliente. a través del diseño de ingeniería, hasta la fabricación y el control.
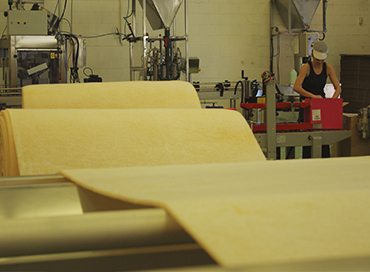
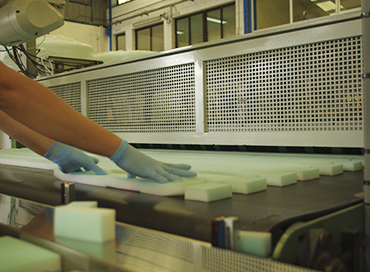
Estado actual y requisitos de la producción
La producción de esponja comienza con los requisitos del cliente que se utilizan para crear las dimensiones de la mezcla y la esponja. Se genera un plan de proceso de la esponja que define el orden y las restricciones (es decir, solución química, PH, etc.). Con base en las órdenes de producción semanales o diarias, el cronograma diario se genera para todos los materiales semiacabados que se deben producir en un día determinado.
El cronograma se almacena centralmente en el sistema heredado. En caso de cambios imprevistos en la calidad o defectos, el cronograma debe ser actualizado. Sin embargo, esto no se puede hacer de manera automática ya que los sensores y los datos de producción actualizados faltan en el sistema centralizado. Luego, las decisiones las toma el Gerente de Operaciones que, utilizando su propia experiencia, propone un nuevo cronograma o la producción se detiene para algunas máquinas hasta que se resuelva el problema o centralmente también con participación humana que introduce datos actualizados, se puede producir un nuevo cronograma de producción.
En el experimento, proporcionaremos CPPS para controlar en tres niveles: ambiente (temperatura, humedad, …) datos de la máquina (revolución de velocidad, picos de voltaje, contadores, … y material principal (altura, densidad, conductividad, …) a la meta, basado en la alineación correcta de un proceso de corte ZD.
Objetivos
- Implementación de gestión de cero defectos.
- Gestión de pedidos de fabricación y seguimiento visual de la programación en tiempo real.
- Seguimiento de las tareas de los operadores que fomentan la responsabilidad entre los trabajadores.
- Mejorar y controlar los Costos totales de la compañía y los Costos únicos de materiales de MOC.
- Eliminar el papeleo de fábrica.
- Notificación automática de alarma por SMS o correo electrónico para informar sobre incidentes que afectan los procesos.
- Enlace de información bidireccional con cualquier programa ERP.
- Prevenir y avanzar las condiciones futuras para evitar problemas importantes del proceso.
KPI de negocios
Todos los KPI de negocios se aplicarán a la línea de producción en el ámbito del proyecto CPPS4ZDM.
Calidad
ZDM (Calidad). La calidad tiene en cuenta los defectos (incluidas las piezas que requieren Retrabajo). Un puntaje de calidad del 100% significa que no hay defectos (solo se están produciendo partes buenas).Reducciones (Calidad). La calidad tiene en cuenta los encogimientos. Un puntaje de Calidad de contracción de 0% significa que no hay contracciones y (todo el material principal se desperdicia en el proceso de producción).
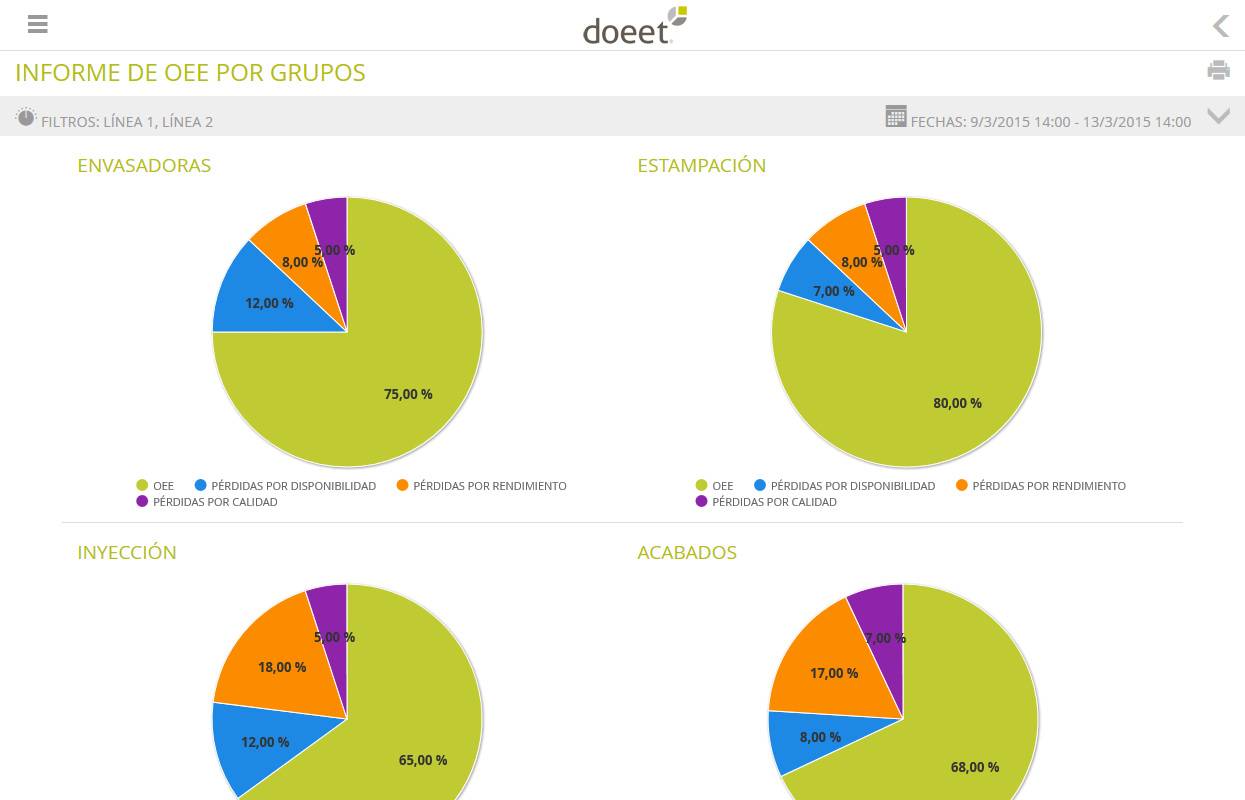
Eficacia general del equipo
OEE toma en cuenta todas las pérdidas. Una puntuación de OEE del 100% significa que solo está fabricando Good Parts, lo más rápido posible, sin Stop Time.
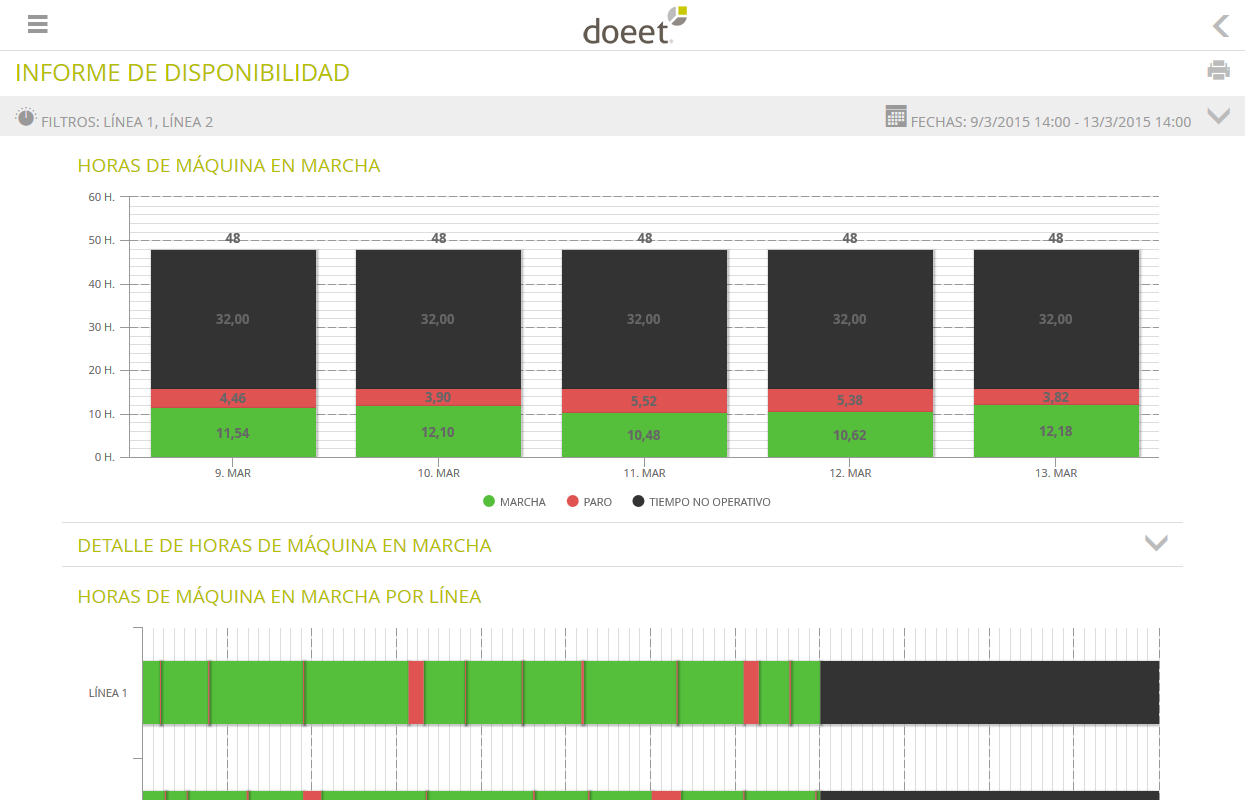
Disponibilidad
La disponibilidad tiene en cuenta paradas no planificadas y planificadas. Una puntuación de disponibilidad del 100% significa que el proceso siempre se está ejecutando durante el tiempo de producción planificado.
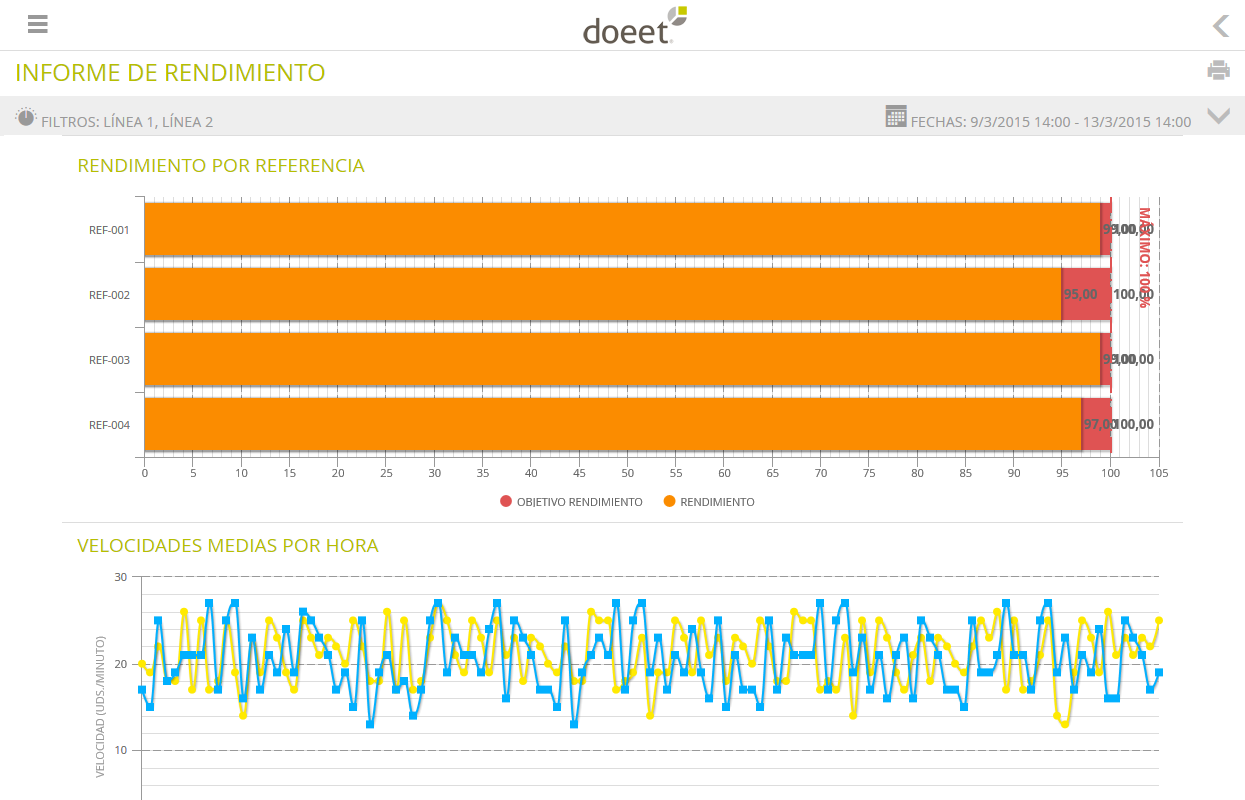
Rendimiento
El rendimiento tiene en cuenta ciclos lentos y paradas pequeñas. Una puntuación de rendimiento del 100% significa que cuando el proceso se está ejecutando, se ejecuta lo más rápido posible.
Resultados esperados y beneficios.
El principal objetivo del experimento CPPS4ZDM es resolver un requisito de gestión de defecto cero con la tecnología BeinCCPS, pero este experimento aportará una amplia gama de beneficios comerciales generales a las PYME que siguen esta implementación:
- Competitividad sostenible. La combinación desafiante de flexibilidad con productividad, precisión y fabricación de cero defectos será llevada a un nivel superior por CPPS, generando respuesta al mercado, calidad, eficiencia, productividad y manteniendo el liderazgo de las PYMES en sectores manufactureros clave.
- Crear lugares de trabajo sostenibles, seguros y atractivos. Se crearán nuevos puestos de trabajo de alta tecnología en la fabricación en torno a estas habilidades, ya sean fabricantes, proveedores de maquinaria y materiales, constructores de fábricas, empresas de automatización o TIC. La estabilización y la mejora de las cifras de empleo en la industria manufacturera impactarían más que cualquier otro sector, no solo en tamaño sino también en trabajos de «derrame» en los servicios de apoyo.
- Los resultados del proyecto de fabricación ambiental con cero defectos reducirán los rechazos, los casos de prueba y los productos básicos. En otras palabras, reducciones del consumo de materias primas que tienen un impacto directo en los costos de producción y reducen la dependencia en el suministro de energía, hasta ahora generación de emisiones y desechos peligrosos.